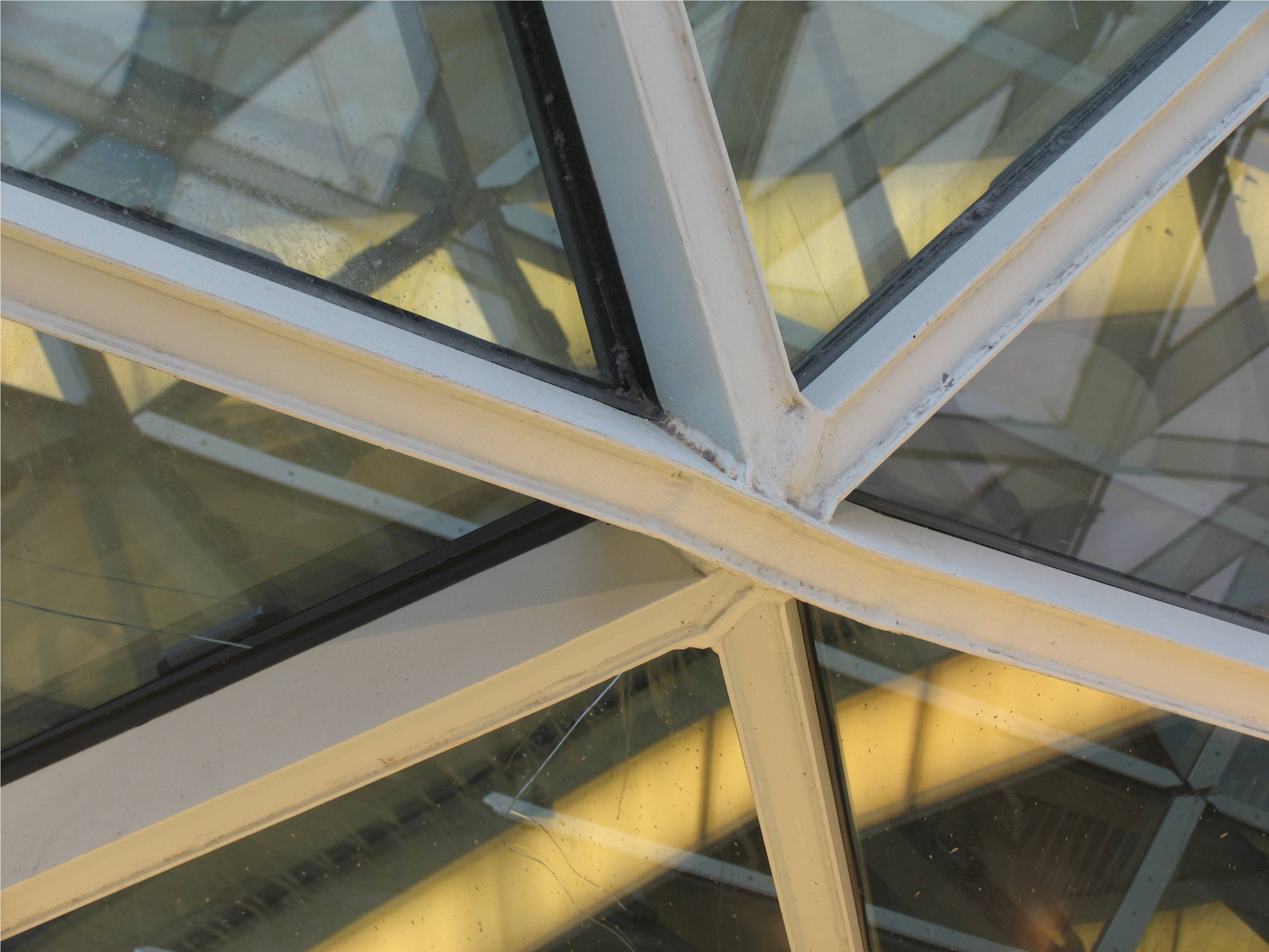
Messy welding
At first sight the roof of the shopping center in the Palaisquartier in Frankfurt has the looks of a nonstandard structure. But look carefully, the detail is welded with very low precision. In the design stage there was the nonstandard concept design of the renowned Italian architect Massimiliano Fuksas, there had been an intentional 3d wireframe mesh, but it was erroneously not executed using a precisely controlled CNC production process. Apparently the steel structure was manually drawn in 3d, not generated by scripts as it should have been. Many of the steel components were cut to length on site, the pieces were welded together on site in an extremely brutal fashion. I feel obliged to show this example for educational reasons, not to blame anyone in this project, not the architect, not the engineer, not the manufacturer. But it is obvious that something went wrong. The link between the file and the factory was broken. There should have been an immediate link from a scripted high precision detail to the with high precision CNC produced components, to be dry assembled on site with zero tolerance. It should absolutely have been avoided to be welded on site since that introduces so much imprecision. Unfortunately, I have experienced a similar problem while building the CET in Budapest. In much the same way that the construction designs of the Bird´s Nest and the Water Cube in Beijing have been compromised by a traditional construction approach, also the execution of the CET has regrettably been subject to old school construction methods. The problem is how to secure a sustainable nonstandard design and building process. The solution is to secure an unbroken link from BIM to CNC production to dry montage of the unique pieces of the 3d puzzle. Breaking the direct link, that is not transmitting the exact data from the “design” phase into the “build” phase of the design & build process, is a recipe for putting back innovation in the building industry.